A Flexible Scheduling System
Repetitive Manufacturing gives you the flexibility to adjust repetitive production schedules as often as necessary and with minimal user intervention. The solution also takes intervening factors, such as fluctuations in production capacity and changes in demand patterns, into account, making the whole process much more efficient.
Performance Visibility
To ensure that you always have immediate visibility to actual performance, Repetitive Manufacturing keeps track of production progress. As unit completions are recorded, deviations and cumulative totals-by-period can be compared to the scheduled rates and quantities, alerting you to take timely corrective action if necessary. Preferences in the way this information is presented can be accommodated using the grid configuration capabilities.
Just-In-Time
To support a ‘Lean’ factory – inventories are ‘pulled’ to each production location on an ‘as needed’ Just-In-Time basis. With Repetitive Manufacturing, you have all the tools you need to identify the net inventory requirements at each production line, unit or cell and to manage the pull of the inventories required at the line-side in order to sustain the scheduled production rates.
Mass Customization
Repetitive Manufacturing schedules allow you to maintain a unique bill of materials and routing for each part being manufactured. The system automatically uses the current version in effect, or you can perform an online override and create a modified version of the current bill of material and routing. You can tailor product configurations as needed to respond to current production conditions or to meet unique customer requirements.
Outside Processing
Given the increased use of outsourcing, outside processing may very well be a part of your planned routing. Repetitive Manufacturing gives you the ability to schedule outside processing by external suppliers into your repetitive manufacturing process. This job step can be easily integrated into the repetitive line.
Work-in-Process Financial Visibility
Repetitive Manufacturing gives you clear and accurate visibility into your current production investment. You have the option to have each schedule provide an online valuation of value-added costs for material, labor, machine, overhead, and outside processing operations.
The total value of completed items is tracked for easy comparison against estimated costs. All transaction activity is tracked for posting and reporting to provide a complete financial view.
Repetitive Schedule Capabilities
- Multiple assembly schedules per production line
- System-generated or manual schedules
- Repetitive flow rate by item
- Production quantity by interval
- Multiple completion dates and quantities
- Ability to automatically create schedules from MPS and MRP planning
- Assembly configuration date effectivity
- Engineering change notices
- Component and operation date effectivity
- One-time component substitutions
- Standard or average cost
- Estimated cost amountsRework code and ship assignment
- Project identification
- Customer and sales order
- Ability to add text/comments
Line-side Inventory Balancing
- Required component inventory based on the current production plan
- Pull tickets generated to direct the required component inventories to the line-side ‘Just in time’ to meet the planned production
- Exception notices for shortages and excess materials
Work-in-Process Transactions
- Time and cost collection for labor, machine, outside processing and scrap
- Lot and Serial Traceability capabilities
- Unplanned issues for lost or defective items
- Reversals for return-to-stock
- Reclaim by-product materials
Schedule Completions
- Completed units moved to inventory or to work order
- Lot and serial numbers assigned
- Over-building controlled by completion tolerance
- Reversal capability
- Back-flushing from both centralized (floor-stock) and line-side inventory locations
- Back-flushing of components based on effective ‘Configuration date’
Schedule Closes
- Separate manufacturing and financial close
- Reversal capability
- Review open quantities and commitments
- Shortage disposition
- Capability to close short
- Review costs and variances
- Late charges and adjustments
- Update historical cost
Download CrescentOne data sheet to learn more about implementing our GLOVIA G2 Repetitive Manufacturing ERP Module at your company.
DownloadExplore More Capabilities
Select a product category below to see how CrescentOne can improve a particular aspect of your business
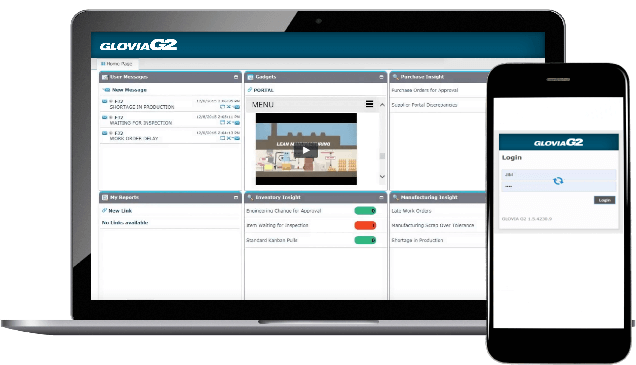