The Value Proposition:
- Minimizes data entry by eliminating the need to enter engineering information more than once.
- Eliminates undesirable data discrepancies and inconsistencies between your CAD/PDM/PLM and ERP solution.
- Eliminates the delay of CAD/PDM/PLM engineering data being made available to your production engineering, planning, procurement, quality and manufacturing teams using GLOVIA G2 ERP.
- Where a significant portion of the business is Engineer to Order, Configure to Order, Build or Assemble to Order this is particularly important in minimizing delivery times – thus helping you to remain competitive.
- The business benefit of the PDM interface soon adds up!
- A reduction in the effort, time and costs involved in Recovering from expensive errors that result in quality issues, scrap, excess inventory and customer satisfaction issues due to late deliveries and product returns and recalls.
- More competitive delivery dates.
- A reduction in the effort, time and costs involved in keeping the information in both systems accurate and consistent.
Features:
Additions and updates to Item Master, BOM and Local Structure information can be exchanged using the interface.
The Color-coded, visual comparison capabilities allow the user to quickly identify the differences between the sending and receiving systems.
The user is provided with the ability to interactively compare and resolve any differences between the CAD/PDM/PLM and GLOVIA G2 solution.
The compact design is focused on user productivity. The user can conduct the whole review, edit and update process from a single screen.
Item defaults and ‘Template items’ provide for the automatic population of GLOVIA G2 Engineering information when the CAD/PDM/PLM solution cannot provide it.
‘Field Picker’ functionality allows the user to identify which of the many, many fields they specifically use. This significantly reduces the information displayed, providing a solution focused on their specific business usage.
Information is exchanged using web services to process standardized XML based documents.
All processed updates are saved to history.
The same business logic and validation that is applied when entering items, BOM’s and Local Structures using GLOVIA G2 screens is applied in the upload and comparison capabilities, thus ensuring the quality and validity of the data loaded into GLOVIA G2.
Download CrescentOne data sheet to learn more about implementing our GLOVIA G2 Product Data Management Interface at your company.
DownloadExplore More Capabilities
Select a product category below to see how CrescentOne can improve a particular aspect of your business
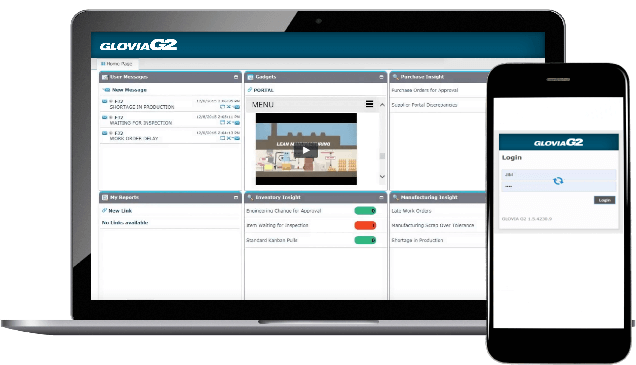