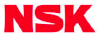
Who:
NSK was founded in 1916 and produced the first ball bearings made in Japan. Since then, the company has spearheaded the development of bearings in Japan. NSK now offers a full range of bearings and sells them worldwide.
Website:
Location:
Head Office located in Tokyo, Japan.
Business Problem:
After a company merger, NSK needed an integrated ERP system to provide a common system across its many plants in Europe, and replace manufacturing systems in five UK sites within an eighteen month period.
Solution:
NSK was looking for a solution that was based on an Oracle/UNIX system and the glovia.com system links with the IBM mainframe bespoke order processing system and PROIV shop-floor data collection system.
Benefit:
glovia.com merges seamlessly with the IBM mainframe and Oracle/UNIX-based system and provides the system support to make NSK a leader in their field.The bearing is one of the great engineering innovations. Without them, the vast majority of machinery and mechanical equipment used in daily life would not be able to function – simple as that. Bearing manufacture is crucial to the world economy and it’s a product that’s in continuous and increasing demand.
The world’s second largest supplier of bearings is the Japanese industrial giant, NSK. Established in 1916, it initially served the home market, it has since grown into a massive international business selling a diverse range of bearings and assemblies. Today, it has offices in 25 countries and a global chain of 30 manufacturing plants.
Moving beyond traditional bearing manufacture, the company has used its precision engineering expertise to expand into automotive and mechatronic products. Its customers now include major Japanese car makers such as Nissan and Toyota. But this diversification also brings new challenges. It puts the company into direct competition with a different type of supplier, and it demands tighter overall control of business performance.
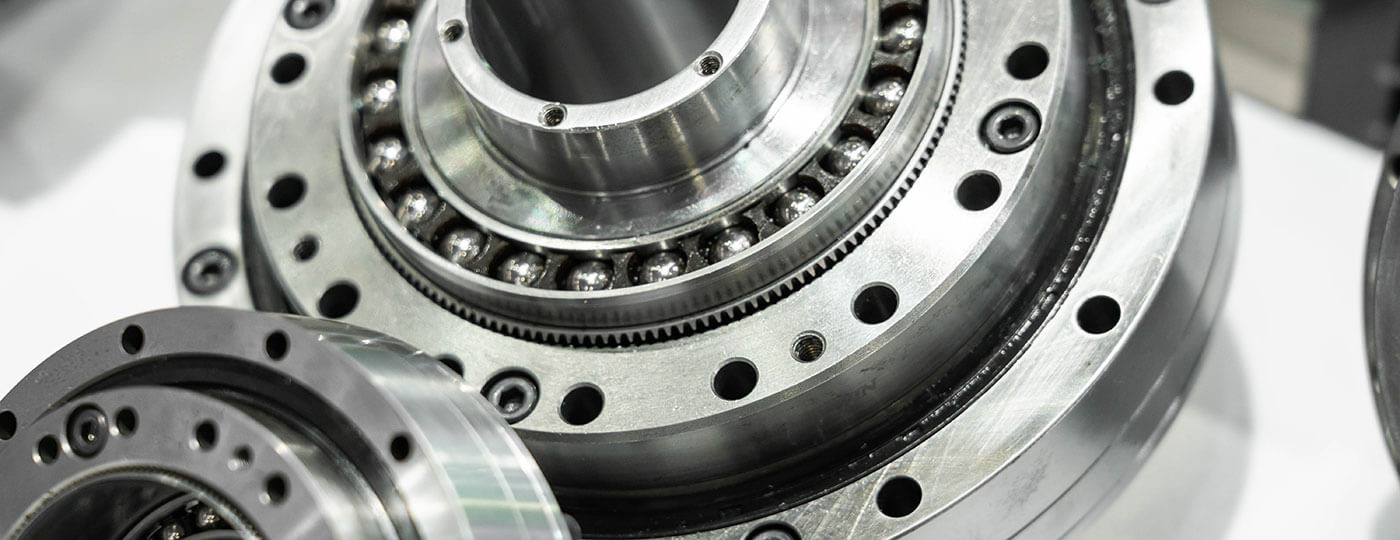
Merger Consequences
In Europe, NSK acquired another major bearing manufacturer RHP. The new organization is now known throughout Europe as NSK. Following the merger, NSK adopted a consistent and coordinated manufacturing strategy across five of its European manufacturing facilities. In particular, they needed an integrated ERP system that would provide a common system across its many plants in Europe. “We manufacture in the UK, Poland, Germany and Switzerland,” says Jack Strong, European Manufacturing Systems Manager. “Some plants, such as the one at Peterlee, have been supplying automotive parts for 20 years. They already had extremely efficient manufacturing processes, so we needed a system that we could shape to fit our processes. What we wanted to avoid was a software solution that imposed constraints on, or demanded changes to, these manufacturing operations.”
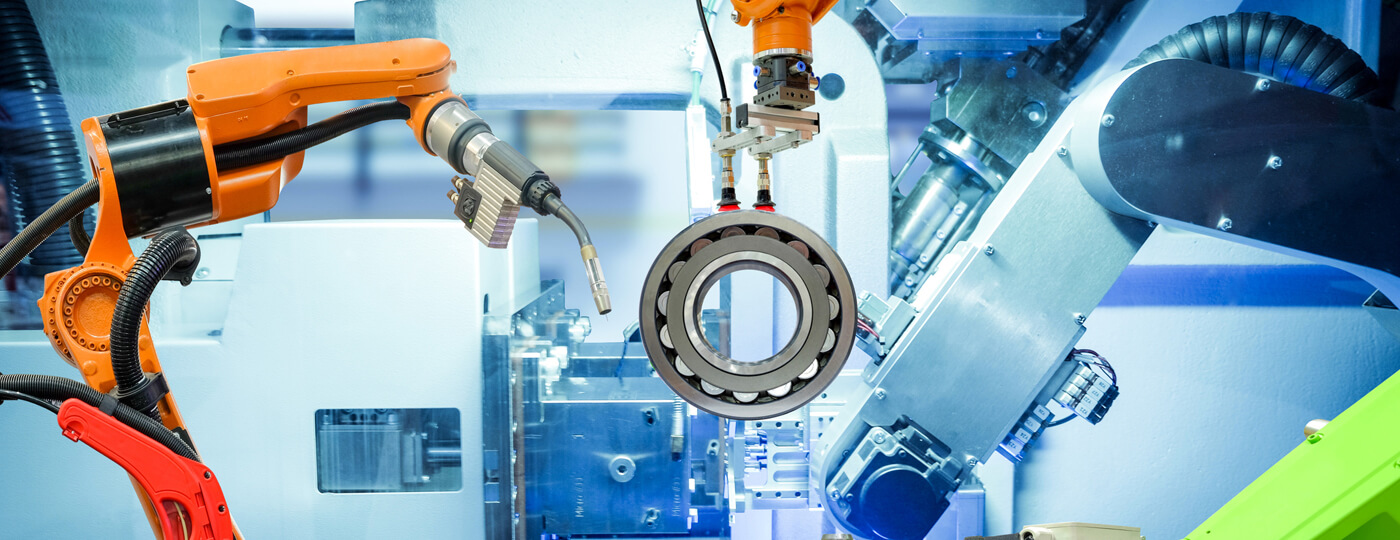
Ease of Implementation
NSK was looking for an Oracle/UNIX-based system and it invited a number of suppliers to tender. This led to a short list of three. The contract was finally awarded to CrescentOne. “The directors felt that CrescentOne was the best fit for our business,” says Strong. “It would be the easiest to implement and – surprisingly – at the time it was the only package that could handle our 27-character part referencing system without modification. All of the other products would have required major rewrites – or we’d have had to re-engineer our business processes from top to bottom.”
Implementing CrescentOne’s ERP product, glovia.com, presented the business team with a tough systems challenge, as NSK needed to replace the manufacturing systems in five UK sites within an eighteen-month period.
The system links with the IBM mainframe bespoke order processing system and PROIV shop-floor data collection system.
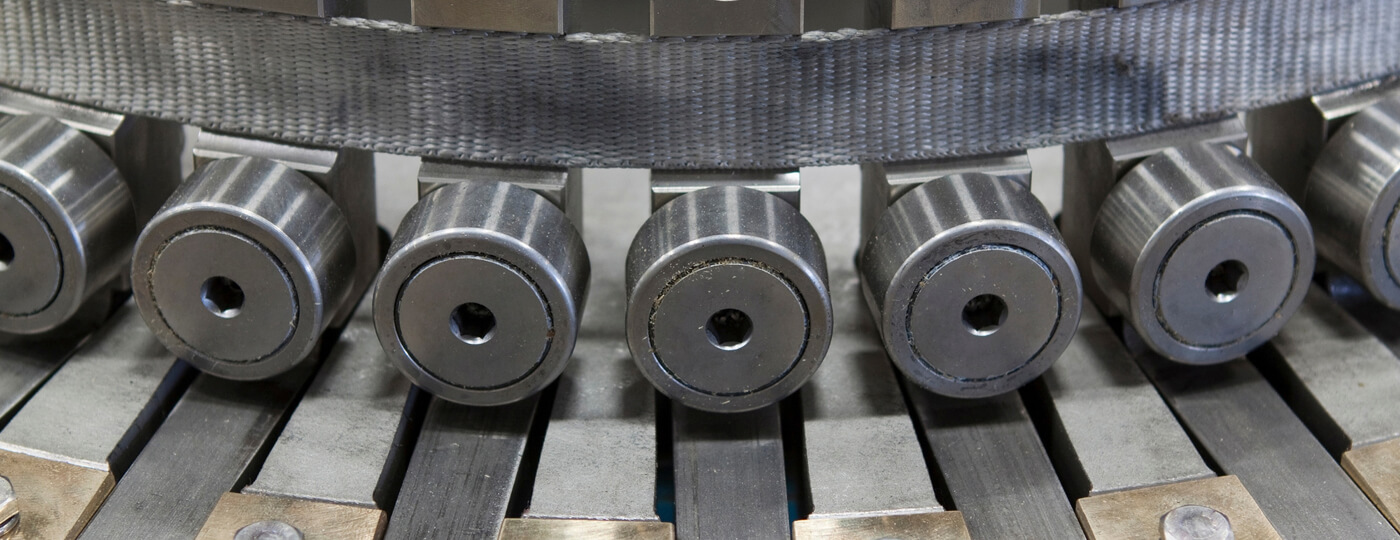
Productivity and Cost Control
Although manufactured to precise specifications, bearings are mass produced products and unit cost is therefore a major consideration. The products are sold to large volume OEM, industrial customers and through third-party distributors in a competitive environment, where purchasing decisions tend to be based on price and availability as well as quality. NSK has to monitor all three parameters constantly, and it must react quickly to market demands, specification changes and technical innovations.
glovia.com provides all the necessary real-time production information, as well as the management reports and statistics needed for delivery, cost and quality control.
NSK now has 500 users across Europe connected to glovia.com. These include a plant in Poland, which was implemented in just six months. Elsewhere in the group, NSK uses glovia.com to control the production of aerospace components.
It would be the easiest to implement and – surprisingly – at the time it was the only package that could handle our 27-character part referencing system without modification.
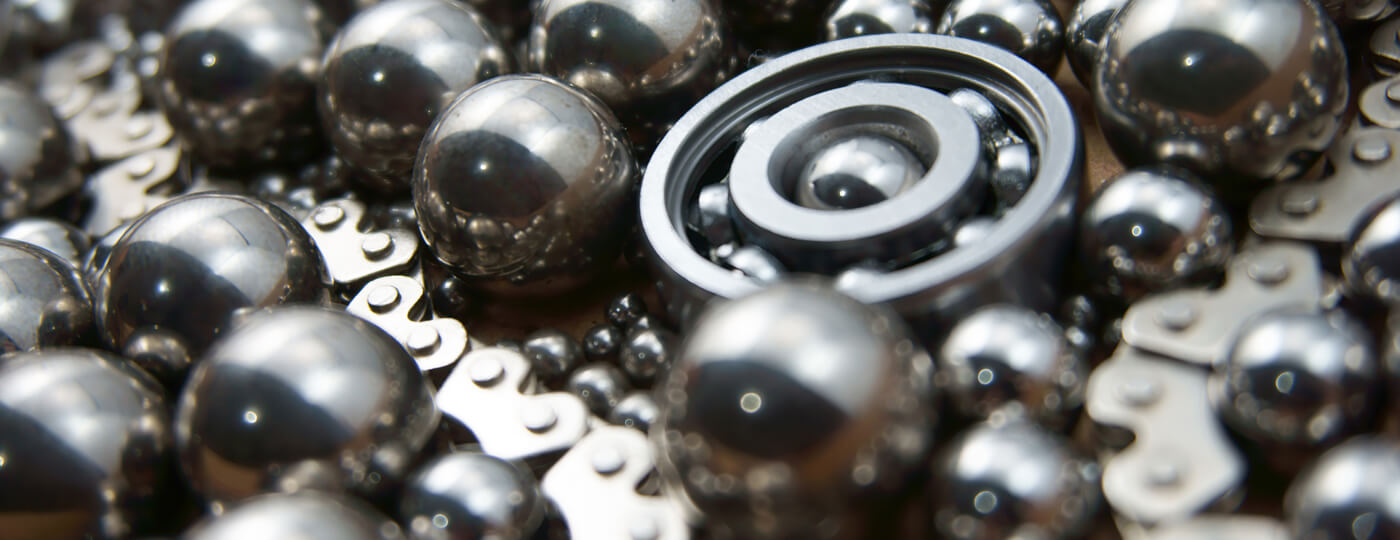
Stock Holding Reduced by £5 Million
Overall, the benefits of the CrescentOne implementation have been significant and wide ranging in our various plants. The external IT support costs have already been reduced by around £1.5 million per annum,” says Strong. “This has been achieved by moving from mainframe platforms to midrange platforms. We have reduced lead times on finished goods, WIP and stocks throughout our factories reducing our stock holding by £5m.
“The penalties incurred by supplying our automotive customers to their strict requirements can be significant and costly. Obligations such as these focus the mind. They tend to ensure that you base your business processes on sound and reliable systems!”
NSK’s reliance on CrescentOne is set to increase in the future; the implementation of glovia.com in its new electronic power assisted steering column plant in Peterlee is an example of this.
“We now thoroughly understand glovia.com and how to implement it quickly and effectively to give us the business benefits that we require,” concludes Strong.